PepsiCo Coventry has been working with MGTS for over 15 years in a really collaborative partnership. Our candidates return from MGTS to go on to really successful careers within PepsiCo. We have had Junior and Mature apprentices following robust programmes, building fantastic logbooks and knowledge on 4 year tailored courses that perfectly prepare them for engineering technical roles. I would recommend any business looking to switch or start their apprenticeship journey with MGTS.
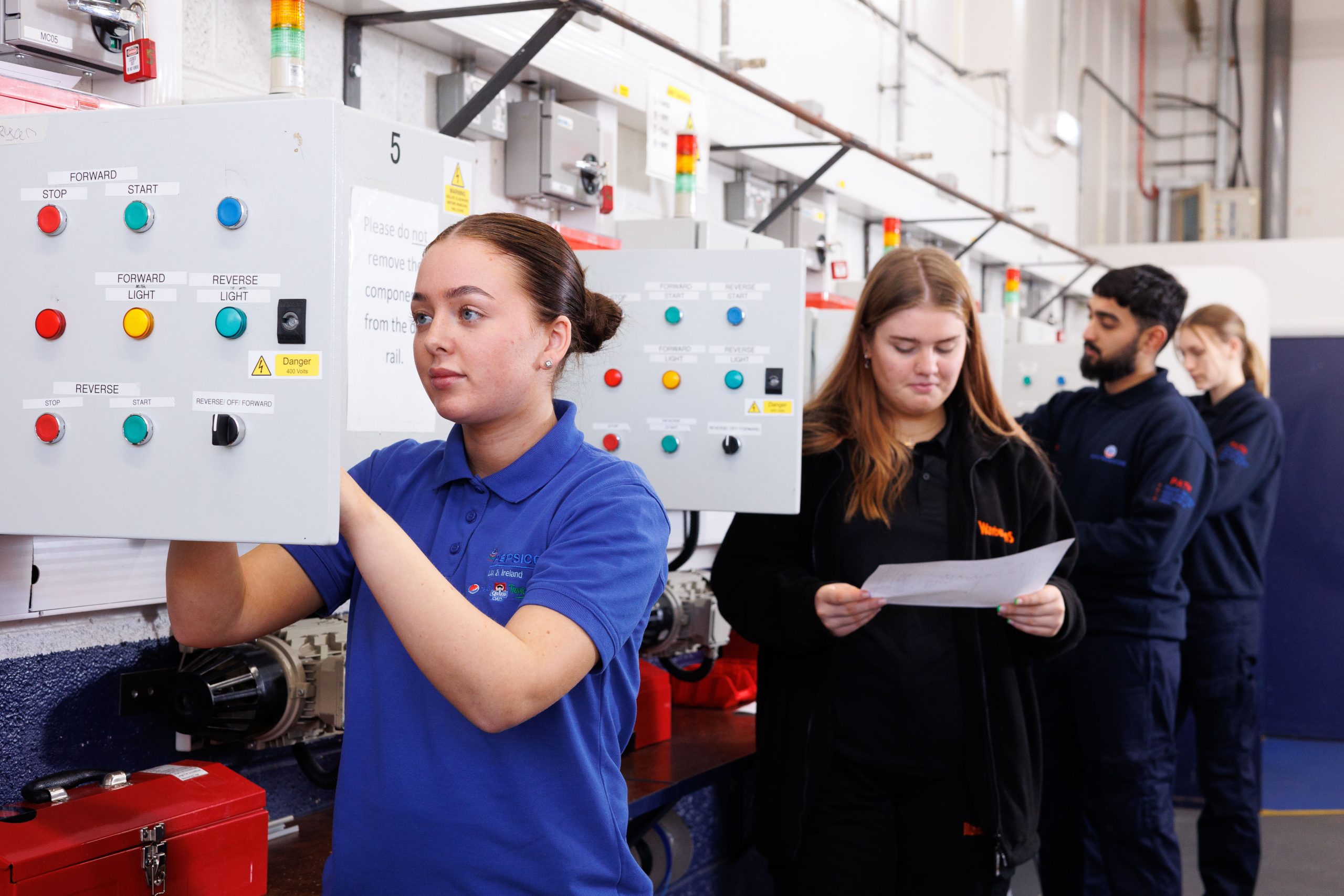
Benefits of offering apprenticeships
- Apprenticeship schemes help employers ensure that they get exactly the knowledge, skills and behaviours they need while growing a talented, motivated and qualified workforce.
- An apprenticeship encourages employees to think of their job as a career thus helping employers with succession planning and staff retention.
- Financial support is available for apprenticeships through the Government Levy.
Year by Year Breakdown
See your Apprentice develop new skills and experience year on year, ready to seamlessly fit into your team.
Year 1
Apprentices spend their first year at one of our Technical Centres learning core practical and theoretical elements of the role.
Employers are introduced to their MGTS Training & Development Adviser (TDA) who will support both the company and their apprentice for the duration of the programme.
Employers have the opportunity to attend a Mentor training course to help understand what skills and knowledge are required to support apprentice progression.
You will benefit from:
- Apprentices develop the appropriate skills, knowledge and behaviours aligned to the job role.
- Operating within a semi-industrial environment MGTS ensure that apprentices are work ready after Year 1.
- Training at MGTS involves developing the necessary work ethics, communication and interpersonal skills and the importance of working to deadlines.
- Opportunity to attend a Mentor Training course.
Year 2
Apprentices return to the workplace to continue their learning whilst attending MGTS on a day release basis to complete the necessary educational requirements for the programme.
Employers select the next stage of training units of the apprenticeship programme with expert guidance from their TDA.
Apprentices complete the BTEC Level 3 Diploma in Advanced Manufacturing Engineering.
Assessment commences to ensure that apprentices are on track to meet the requirements of the programme.
You will benefit from:
- Apprentice returns to the workplace to implement their learning and actively contribute to the success of the business.
- Expert advice and guidance from your TDA when selecting training units for further development in the role.
- Ongoing TDA support for both apprentice and employer.
Year 3
Learning continues within the workplace. The TDA will continue assessing apprentices to ensure that they are on track to meet the requirements of the programme. Where skill gaps are identified training plans will be developed and implemented in conjunction with the employer.
If potential is identified apprentices may commence HNC study.
You will benefit from:
- Identification of any skill gaps to meet the requirements of the programme.
- Advice and guidance on developing training plans.
- Ongoing TDA support for both apprentice and employer.
Year 4
Conclusion of Level 3 workplace competencies.
Apprentices will prepare for the End Point Assessment (EPA) with the support of their TDA.
If potential is identified apprentices may complete HNC study.
You will benefit from:
- Apprentices are ready and prepared to undertake the EPA with a professional engineering institute.
- Completion of Level 3 qualification and workplace training plan.
- Completion of HNC study where applicable.
Our ongoing partnership with MGTS continues to play a vital role in the development of skilled engineering talent within our business. Their expertise, professionalism, and commitment to high-quality training are closely aligned with our own values and standards. Through this collaboration, we have established a strong and sustainable pipeline of capable apprentices who contribute positively to our operations.
We look forward to continuing this successful relationship.
The quality of teaching, learning and assessment is consistently good and supports apprentices to make good progress and succeed well.
In practical training areas, the quality and range of technical resources to support the training of engineering apprentices are impressive.
Apprenticeship Pathways
Our rationale is to work in partnership with employers to identify and solve engineering skills gaps, advising them on the most suitable Pathway for their learners.
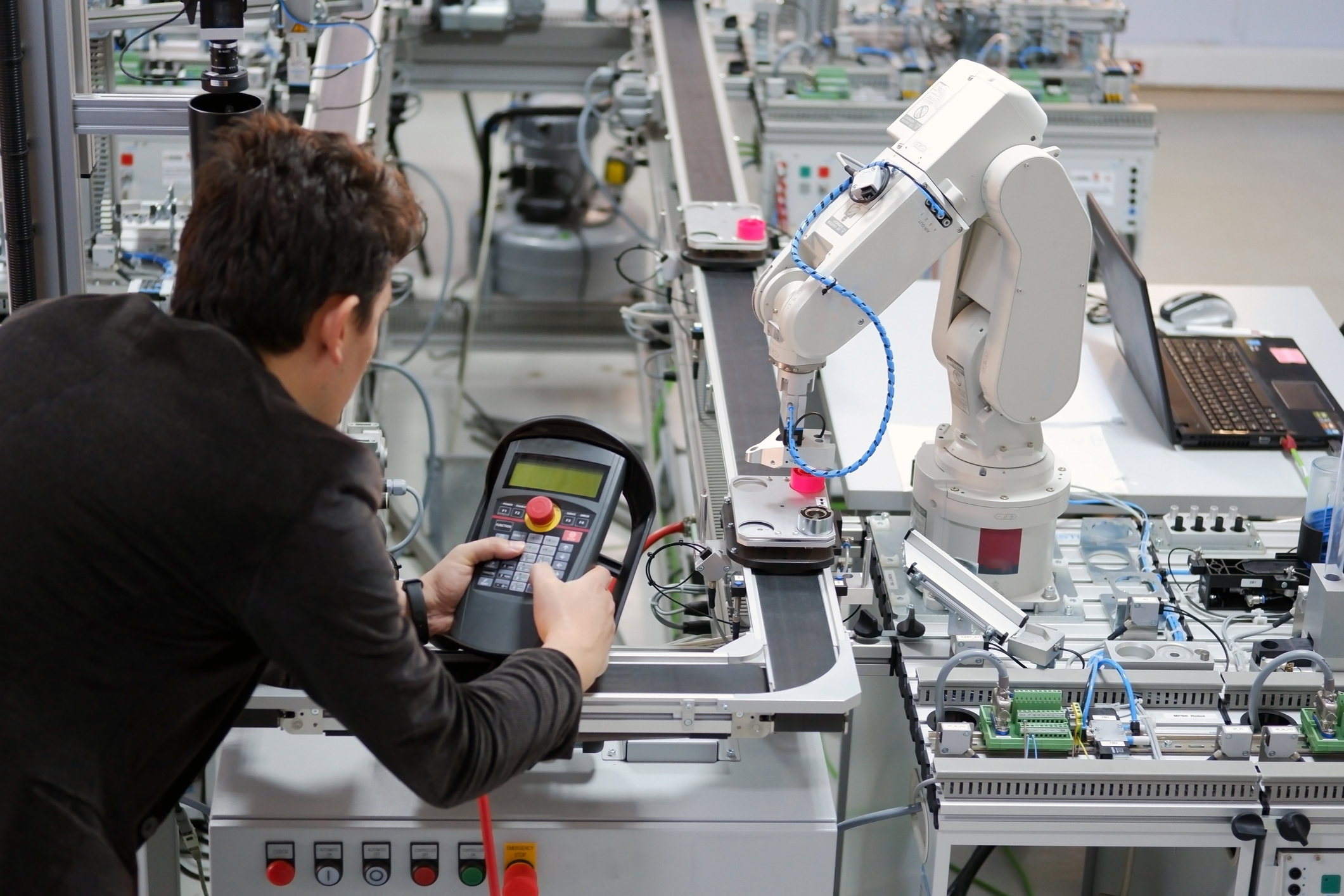
Mechatronics Maintenance Technician
As a Mechatronics Maintenance Technician you ensure that plant and equipment perform to the required standards.
Find out more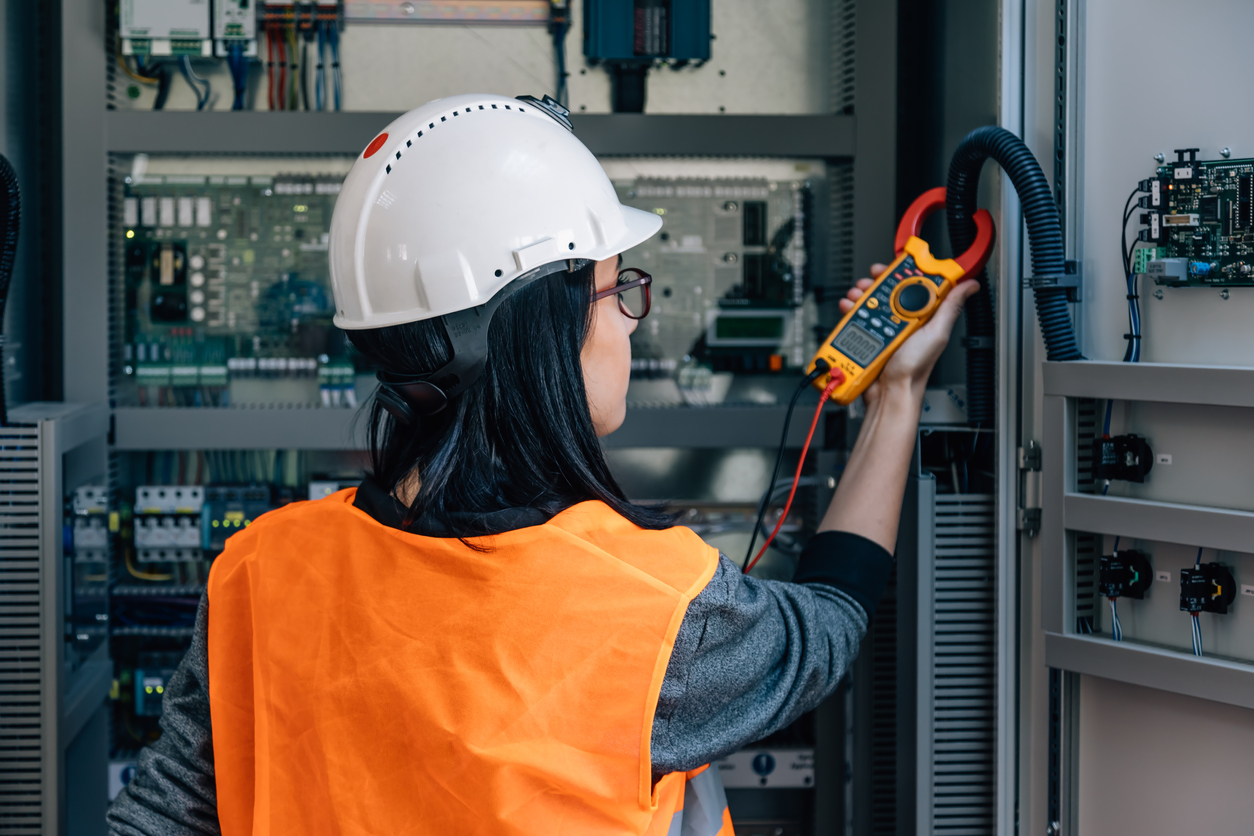
Maintenance and Operations Engineering Technician
Maintenance and Operations Engineering Technicians will maintain the safety, integrity and effective operation of plant and equipment.
Find out more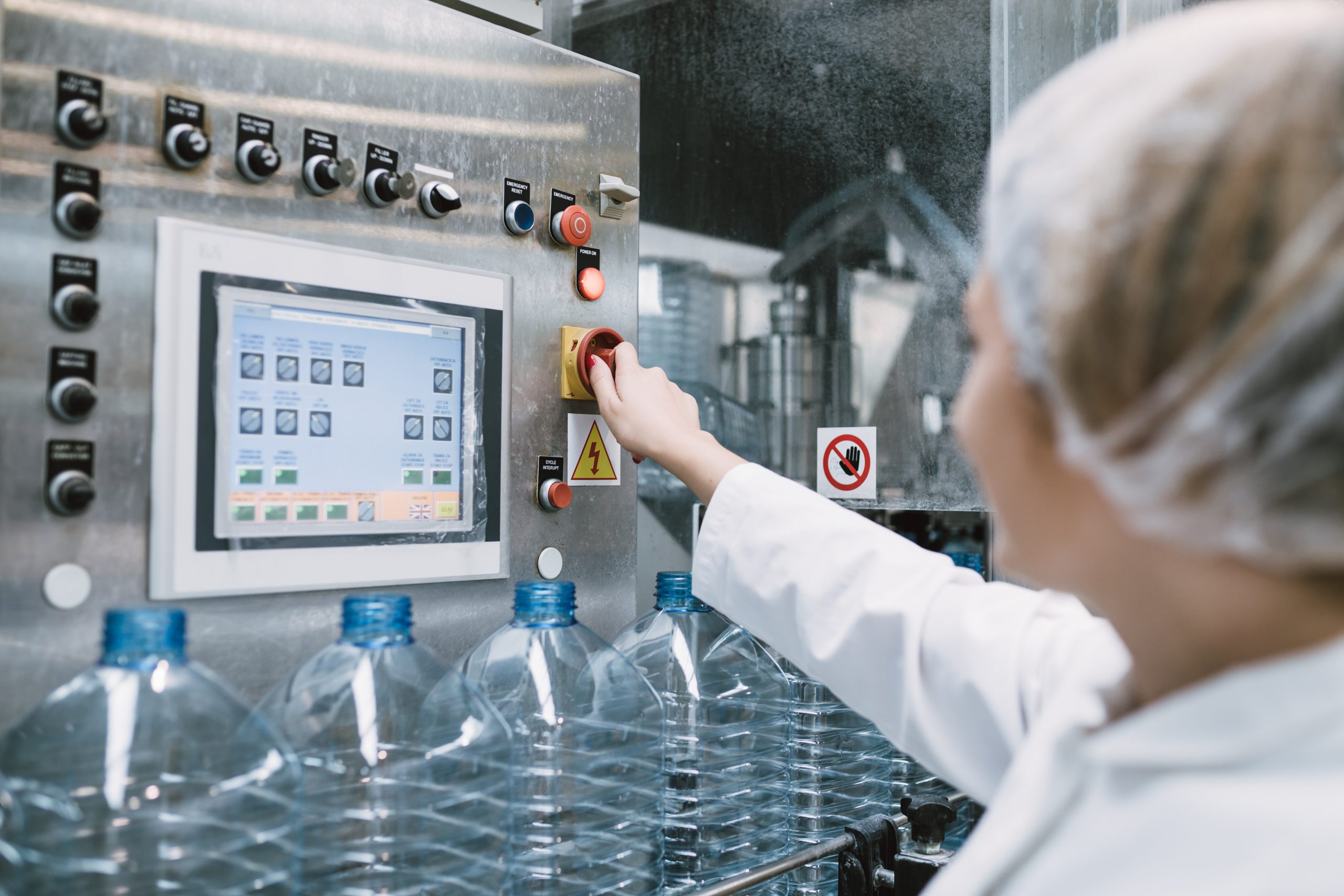
Food and Drink Engineering Maintenance Technician
Food and Drink multi-skilled maintenance technicians will work with mechanical and electrical equipment plus highly automated programmable control systems.
Find out more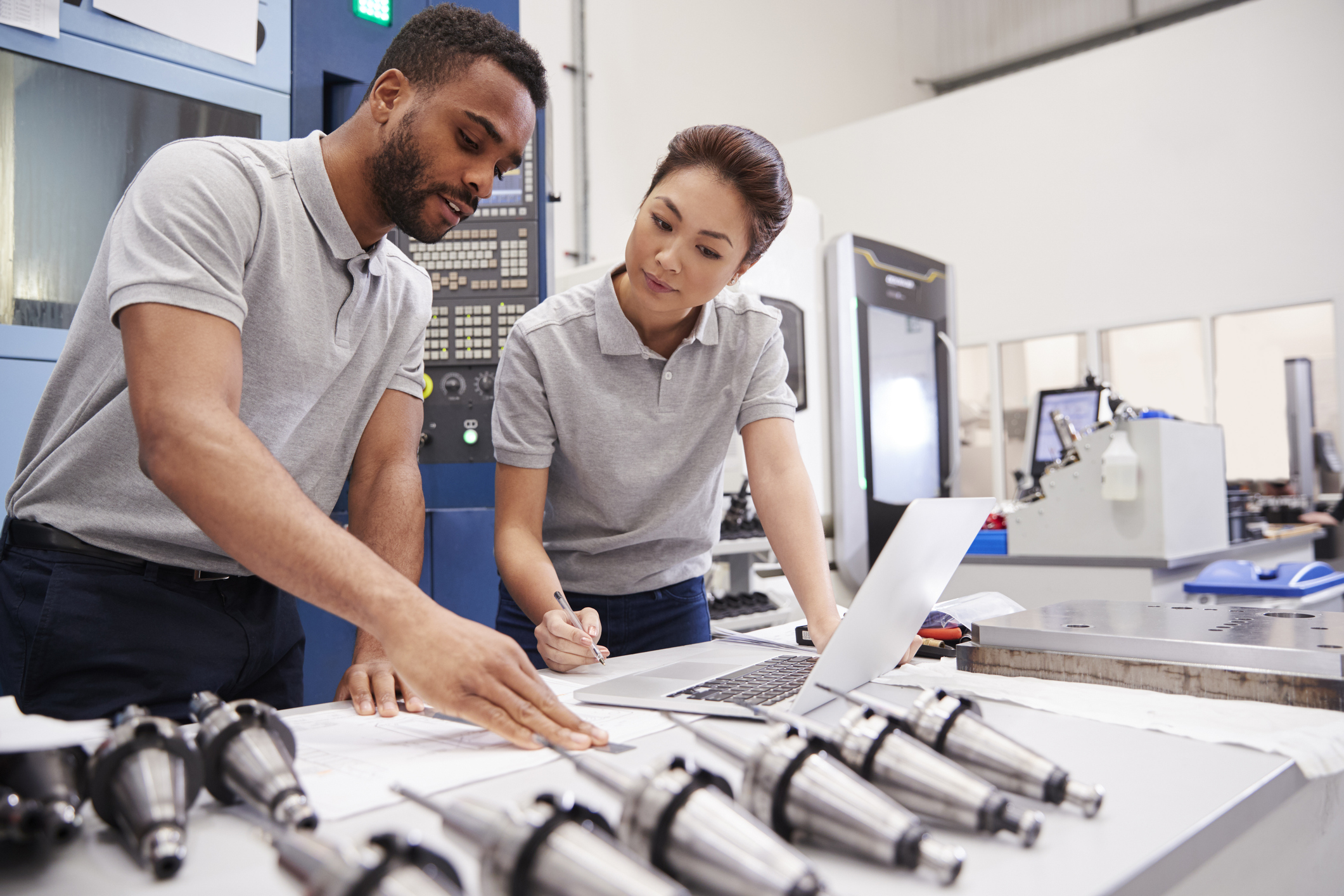
Engineering and Manufacturing Support Technician
Engineering and Manufacturing Support Technicians work as part of a team to provide technical support and expertise for all areas of engineering and manufacturing functions.
Find out more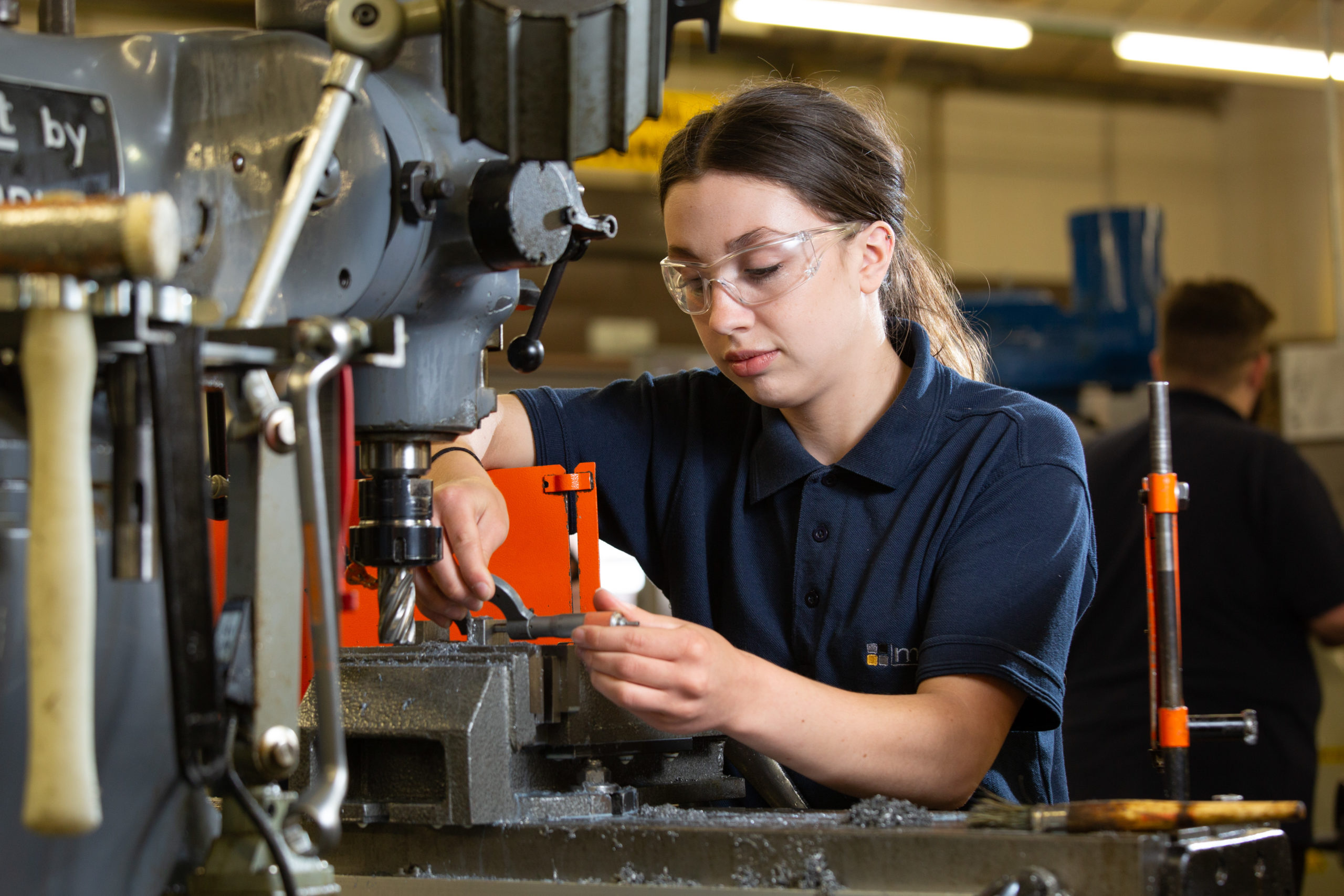
Toolmaker and Tool & Die Maintenance Technician
Toolmakers and Tool & Die Maintenance Technicians are highly skilled engineers, carrying out complex and specialist detailed work.
Find out more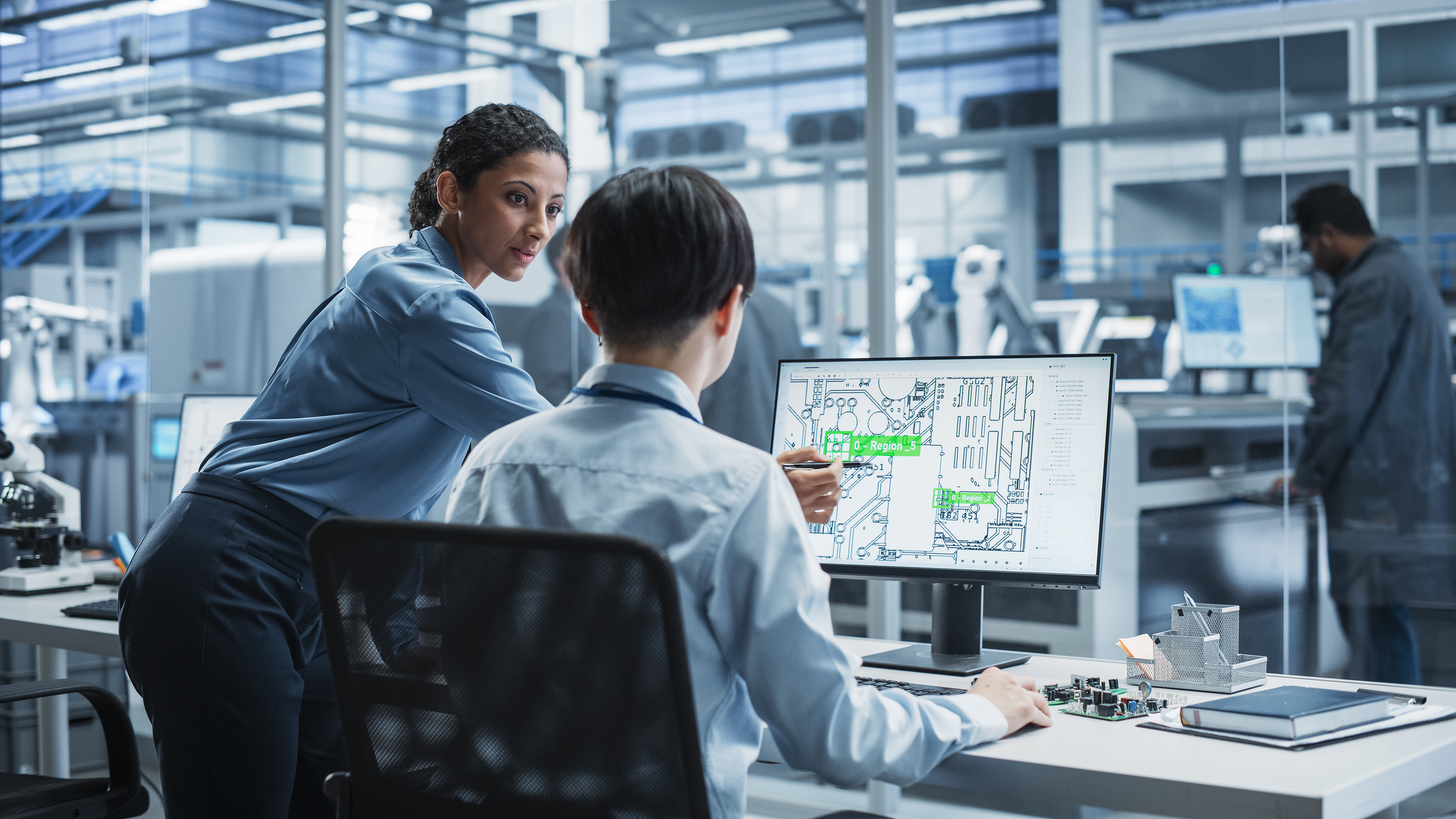
Product Design & Development Technician
Design engineers improve product performance and efficiency while researching and developing new manufacturing ideas and systems.
Find out more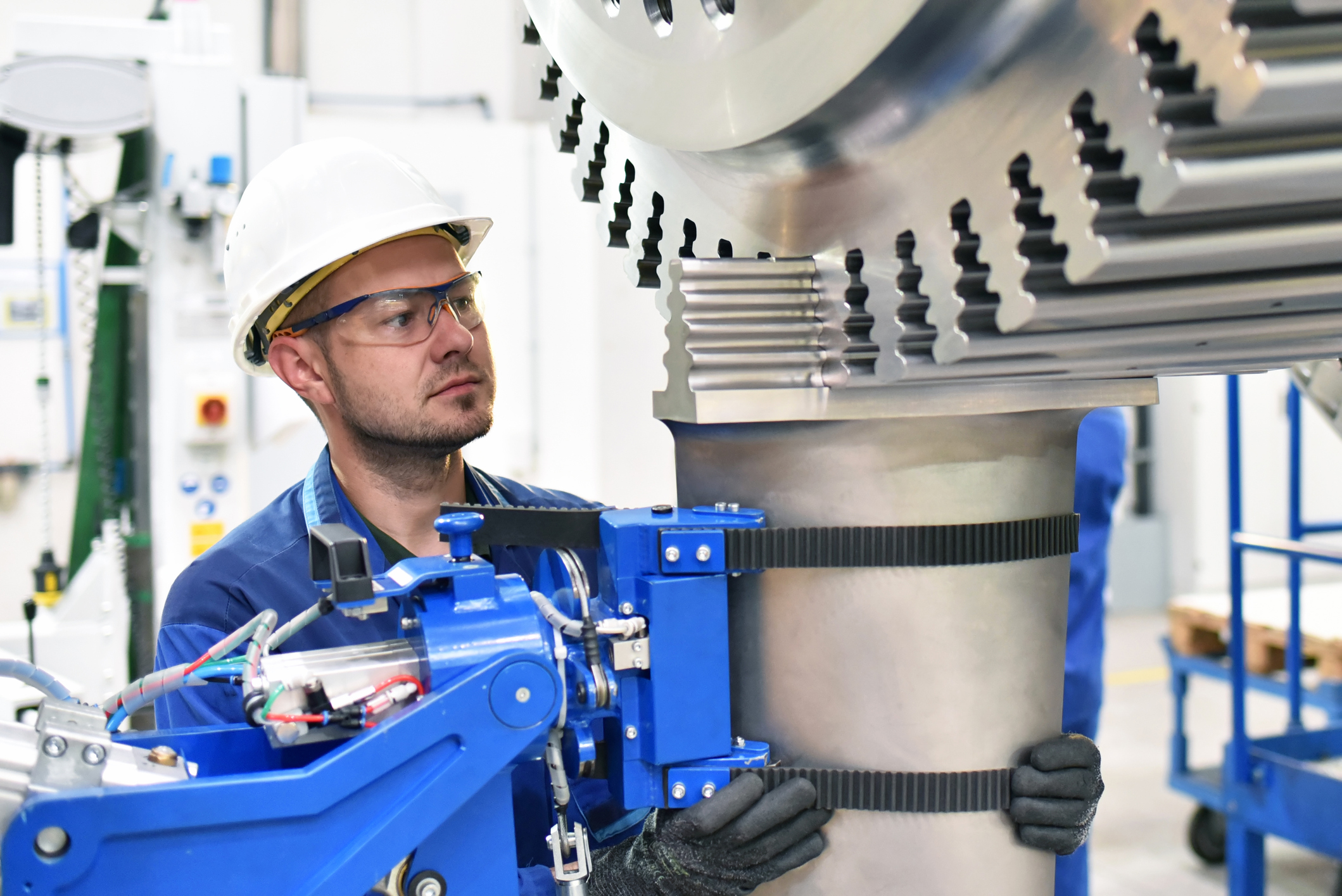
Engineering Fitter
Engineering Fitters produce complex high value, low volume components or assemblies. They will interpret drawings/specifications, plan their work and be required to check against quality standards.
Find out more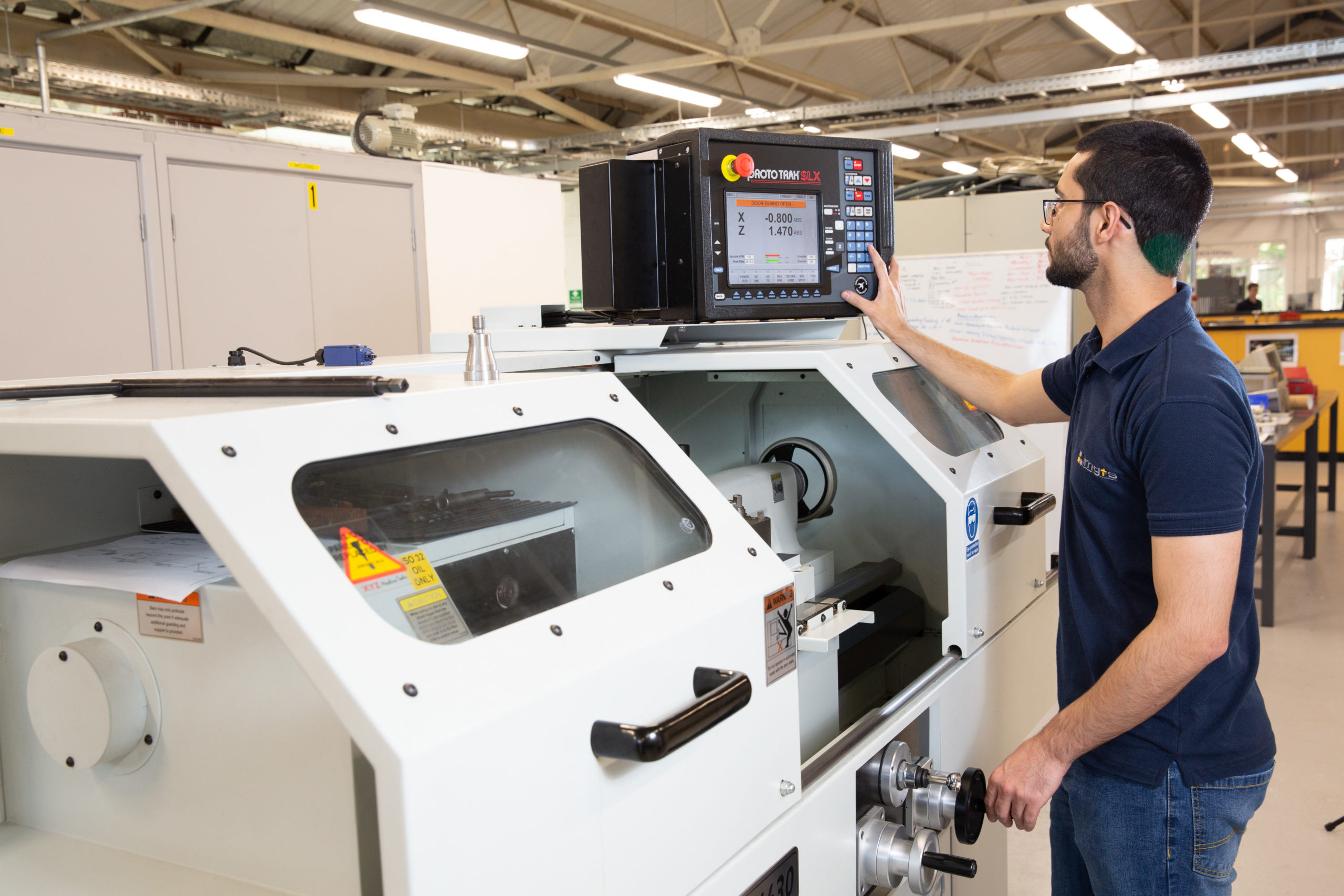
Machining Technician
Machining Technicians create, install, maintain and repair metal products, including machinery and equipment in factories.
Find out more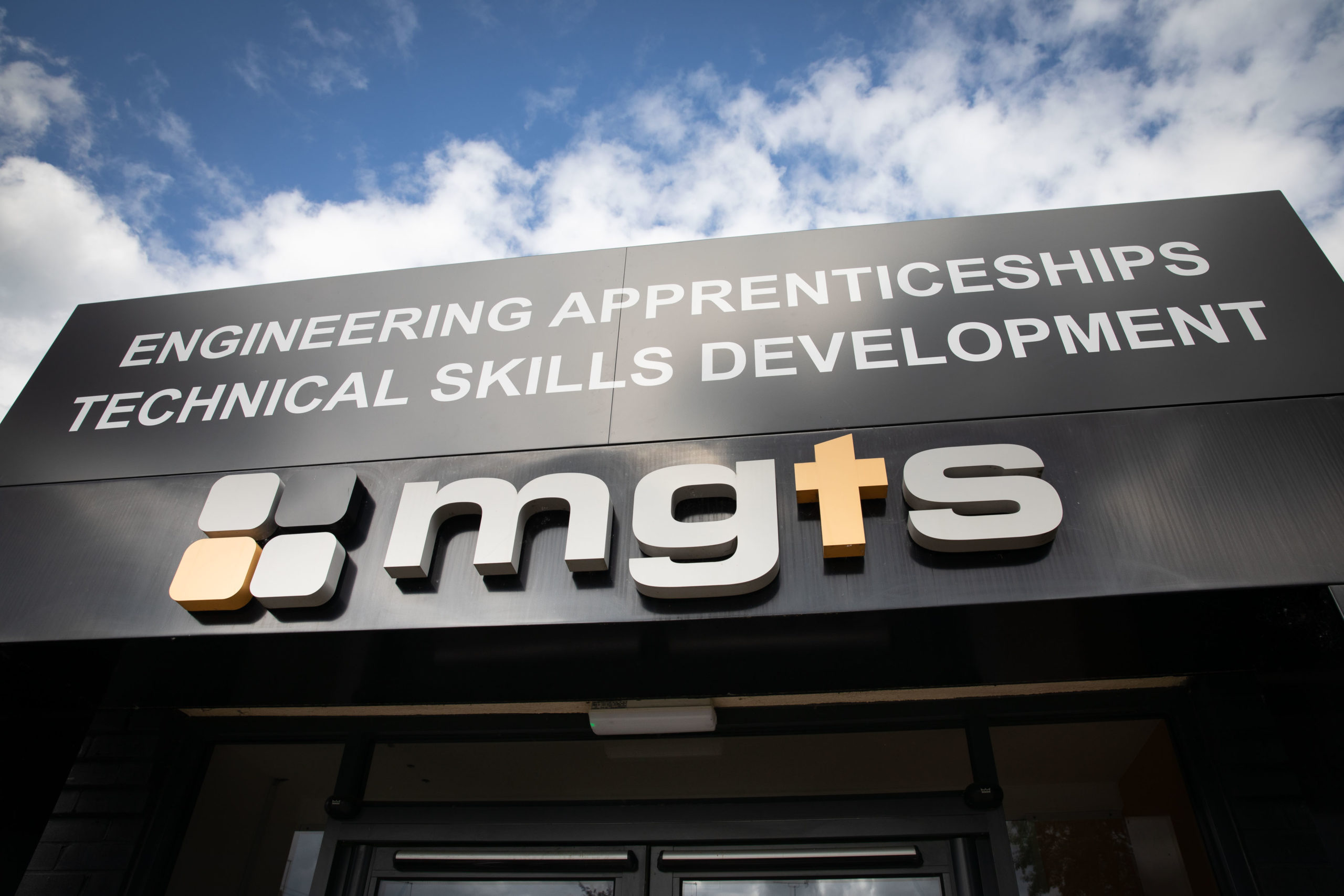
Why MGTS
MGTS is a Centre of Excellence for the provision of engineering apprenticeships with a proven track record of over 50 years. With a client base ranging from SMEs to national operators we have become a trusted brand within industry.
We offer a free recruitment service to source and match high calibre candidates to meet your requirements. Plus all MGTS Technical Trainers are from within industry and are fully qualified engineers with expert skills and knowledge.
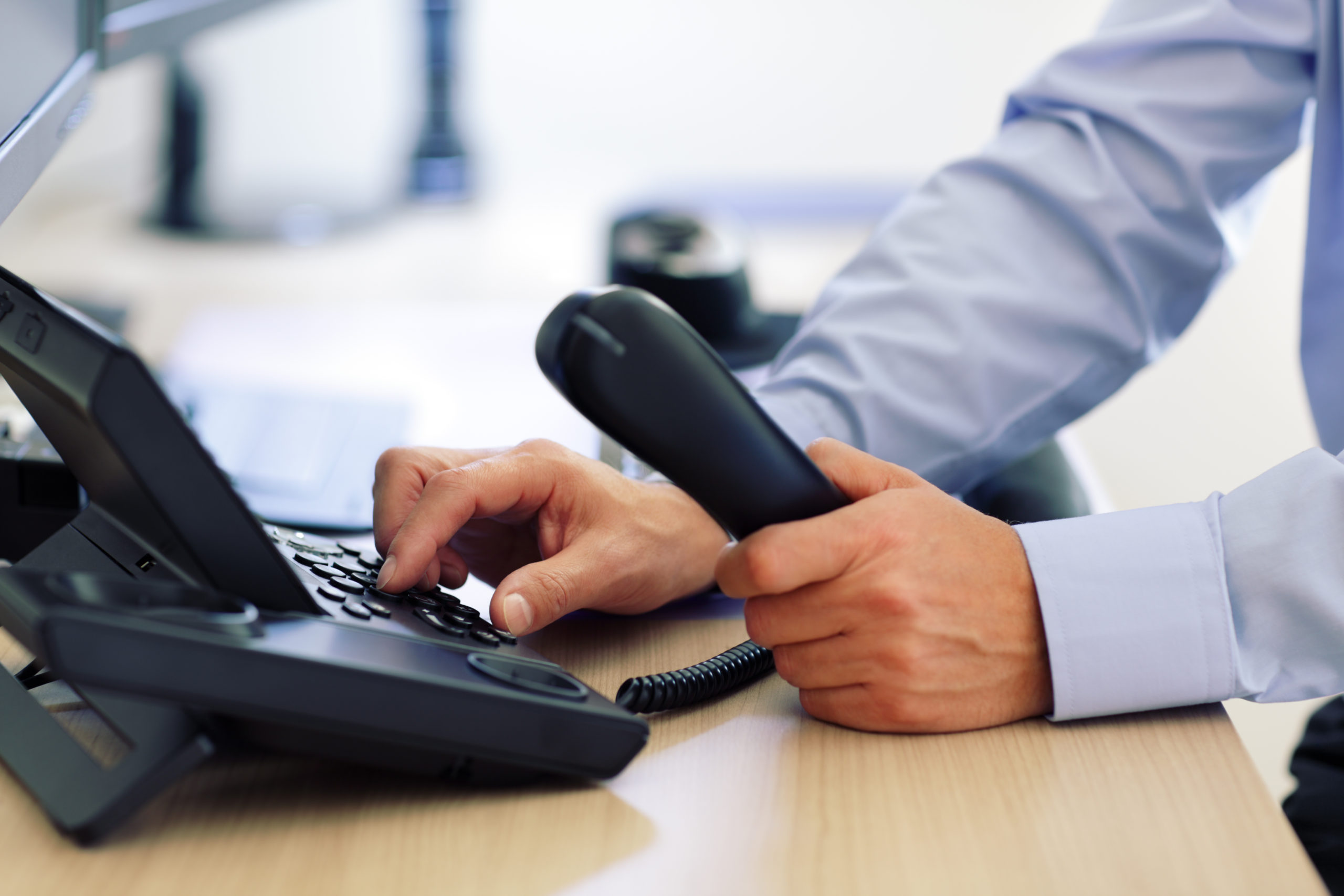
Talk to Recruitment
Our Customer Engagement Team has a wealth of knowledge and experience in supporting companies with their apprentice recruitment journey.
024 7663 0333 recruitment@mgts.co.uk